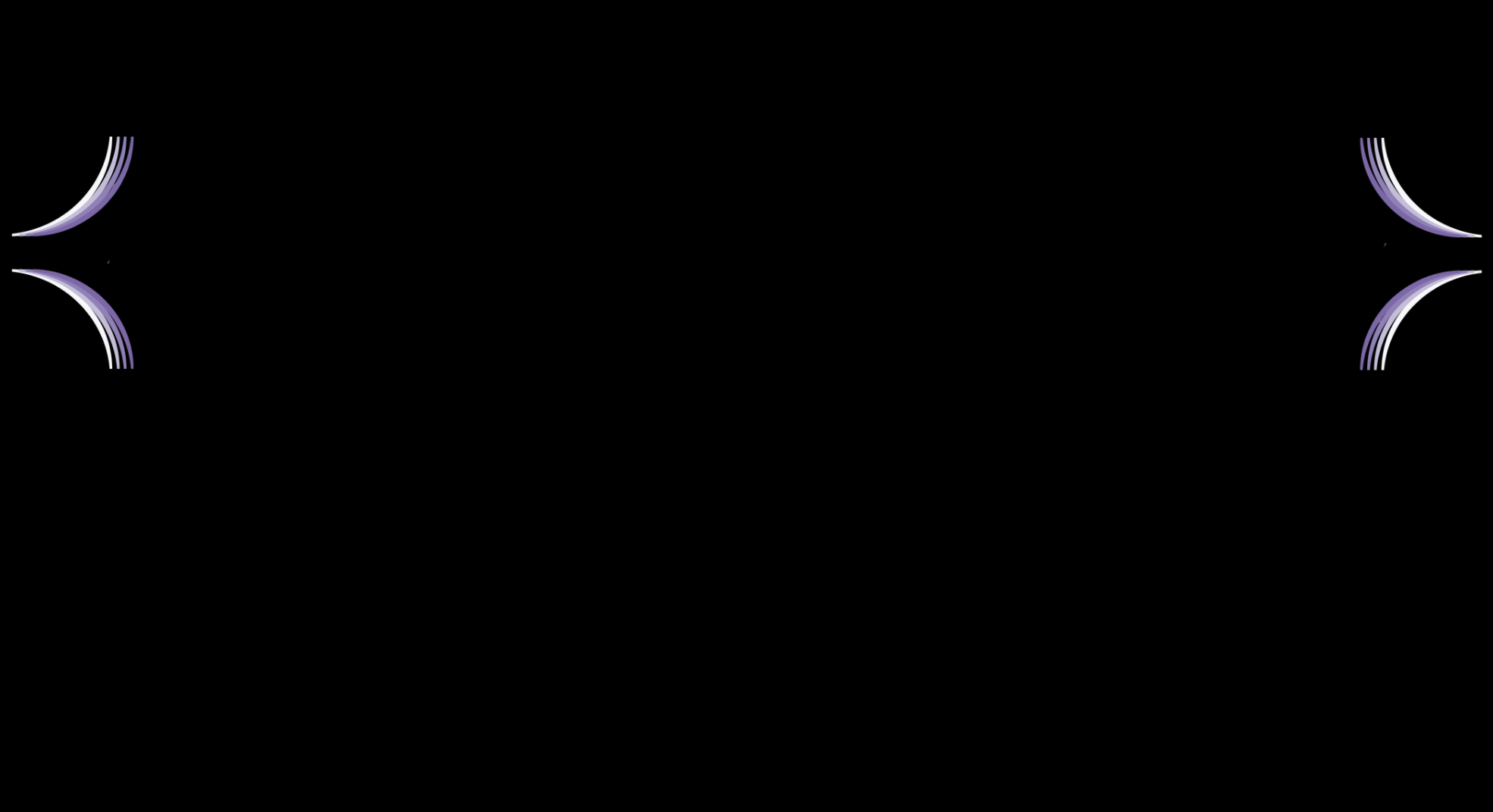
Aerospace and Defence - Why Stereolithography?
Aerospace and defence manufacturers face unique challenges in terms of producing high-quality, intricate and lightweight components whilst adhering to strict regulations. RAPLAS Stereolithography has gained significant attention from these industries due to the ability of our technology to create complex geometries and excellent surface finishes, utilising advanced materials.
Raplas partners with a number of resin manufacturers, giving our customers access to a wide range of materials, including highly specialised bespoke solutions for the Defence industry. For more information on materials contact us at info.uk@raplas.com
By incorporating RAPLAS systems into your manufacturing processes, you can join the industry leading manufacturers in revolutionising your production capabilities.
(Parts printed on a Raplas PR700)
Benefits of stereolithography for aerospace and defence
Stereolithography enables a wide range of parts production through the variety of applications possible with the technology.
Lightweight components
Additive manufacturing offers substantial cost savings through material reduction and optimised design processes. By utilising internal lattice structures, additive manufacturing enables the creation of lightweight parts, which can result in reduced fuel consumption and lower carbon emissions for aircrafts. This weight reduction not only enhances the fuel efficiency of aircraft but also contributes to a more sustainable and environmentally friendly aviation industry.
Prototyping
SLA facilitates swift and economical production of functional prototypes. Industries such as aerospace and defence can leverage SLA to craft exceedingly precise parts in a fraction of the time taken by traditional manufacturing methods, thereby significantly reducing lead times.
Tooling
SLA enables the creation of high-quality, custom tooling component such as jigs, fixtures, and moulds. These tools aid in the production of composite parts, reducing the reliance on traditional manufacturing methods. SLA-produced tooling offers benefits such as reduced weight, increased complexity, and improved lead times.
End-use parts
The aerospace and defence sectors are increasingly exploring the potential of SLA for end-use parts. The capabilities of SLA technology in producing lightweight, robust, and intricate components offer avenues for optimising designs and elevating overall performance. Coupled with the expansion of compatible materials, including those aligned with the RAPLAS open-source materials solution, a multitude of end-use part possibilities become accessible to our clientele.
Raplas systems benefits for aerospace and defence
Security
Raplas systems have an optional Ultra High Security software developed specifically for the Defence sector to ensure customers data is always secure. For more information on this contact us via info.uk@raplas.com
High precision and repeatability
The RAPLAS PR machine exhibits exceptional precision and part accuracy excelling with production of parts requiring tight tolerances with the capability to perform and produce parts consistently at this exceptional quality.
Scalability
Offering an impressive build platform with a range of sizes reaching up to 800 x 700mm, the RAPLAS PR machine enables the creation of life-size functional prototypes and end-use parts. This remarkable scalability opens exciting possibilities for aerospace and defence manufacturers, as they can now produce large-scale components with ease and precision. By leveraging the size capabilities of the RAPLAS machines, manufacturers can accelerate the development process by creating realistic, full-scale prototypes that accurately represent the final product.
Superior surface finishes
The RAPLAS PR machine ensures superior surface finishes enhancing the overall quality of manufactured components. Aerospace and defence manufacturers can benefit from the reduced time and effort required for finishing operations.